Renovation of worn tools
Give a second chance to your worn out tools thanks to the renovation! You can achieve higher reliability of production process and productivity.
What is the renovation of worn out tools?
We extend the life of the production tools through a comprehensive renovation. This includes, in particular, full service of sharpening, renovation and coating of tools, such as sharpening of milling cutters, drills, countersinking tools, taps and other tools, including special ones. The output product is equipped with grinding according original geometry and a suitably chosen coating as required.
The machining tool corresponds to the required operating parameters and preserves the original geometry. So the tools achieve 100% performance of the new tool.
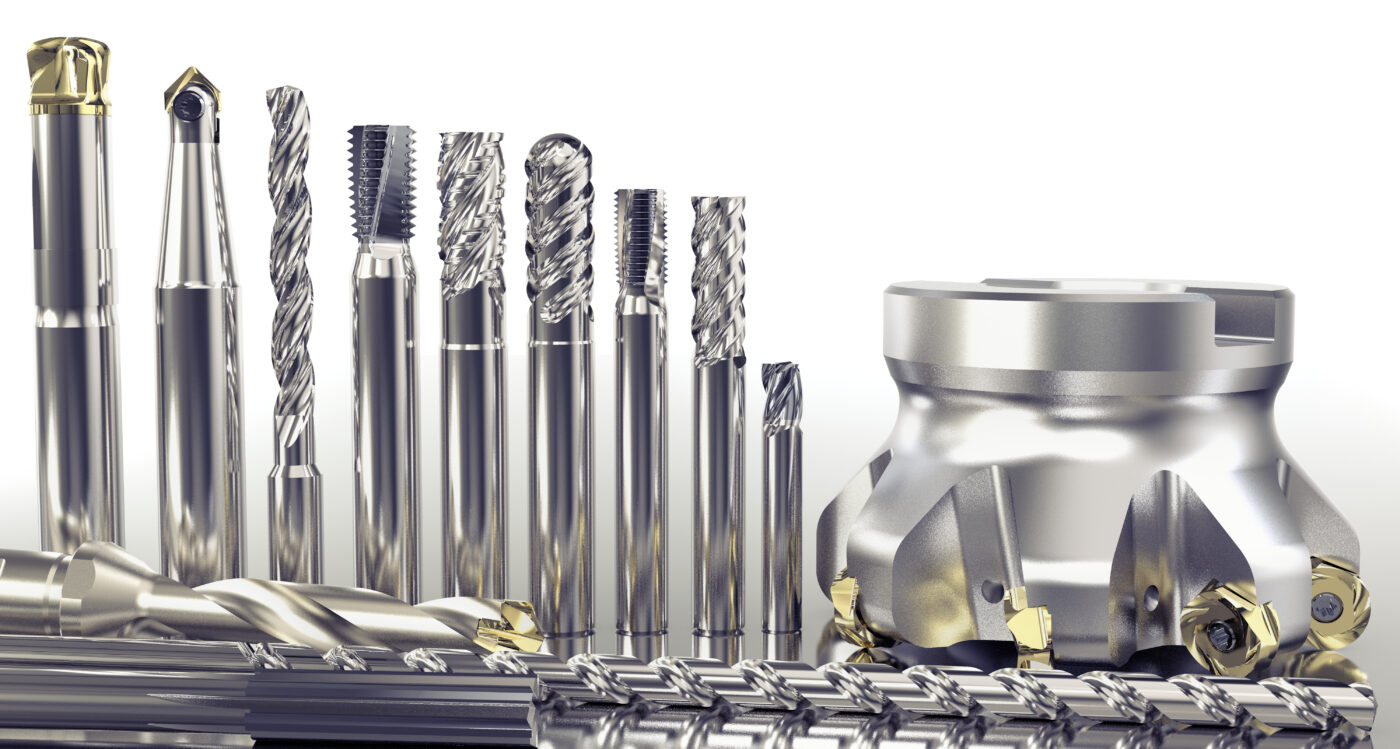
What tools do we renovate?
We provide sharpening of our tools and also tools from other renowned manufacturers.
For sharpening, we use grinders from top companies SAACKE, Deckel and ANCA. In cooperation with external suppliers, we apply high quality PVD coatings on tools. This results in a higher service life, increased cutting parameters and resulting better machining quality.
Can we guarantee the same performance as the new tool?
YES. The tool achieves 100% performance as a brand new tool. Regular maintenance and renewal of the machinery together with technological procedures and experienced staff ensure the required precision and quality of the renovation.
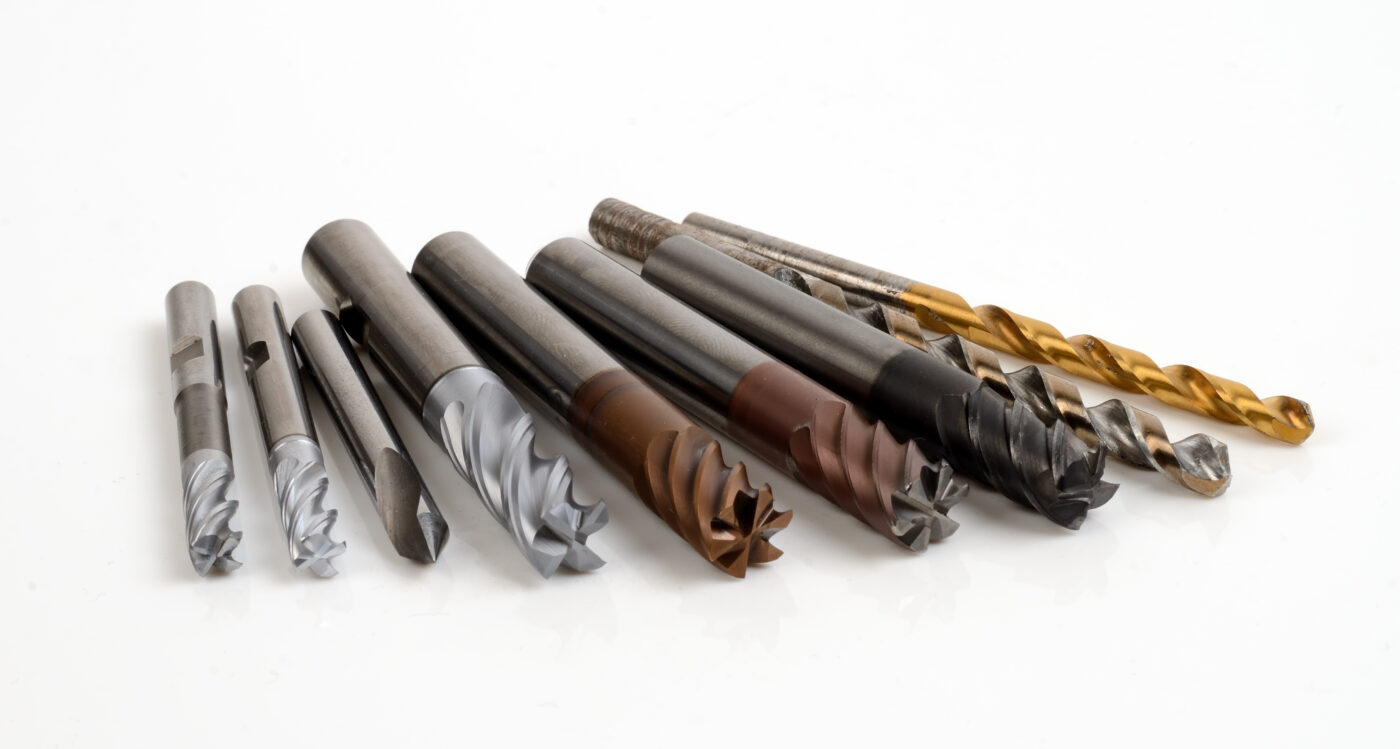
HOW LONG DOES THE TOOL RENOVATION TAKE?
Delivery time for refurbished tools including coating is usually within 10 business days of receiving the tools.
How does the whole process work?
- We will pick up the tools at your factory and store them in a box that is designed for tool renovation and has a unique number for your order.
- We grind your tools to the original geometry, repair, shorten, lighten, we will do everything to ensure that the tool achieves 100% performance as new.
- In the last step, the tools are coated (usually SC and HSS). We will be happy to help you choose the right coating.
- The order is now only checked, and we will take it back to you at the production plant.
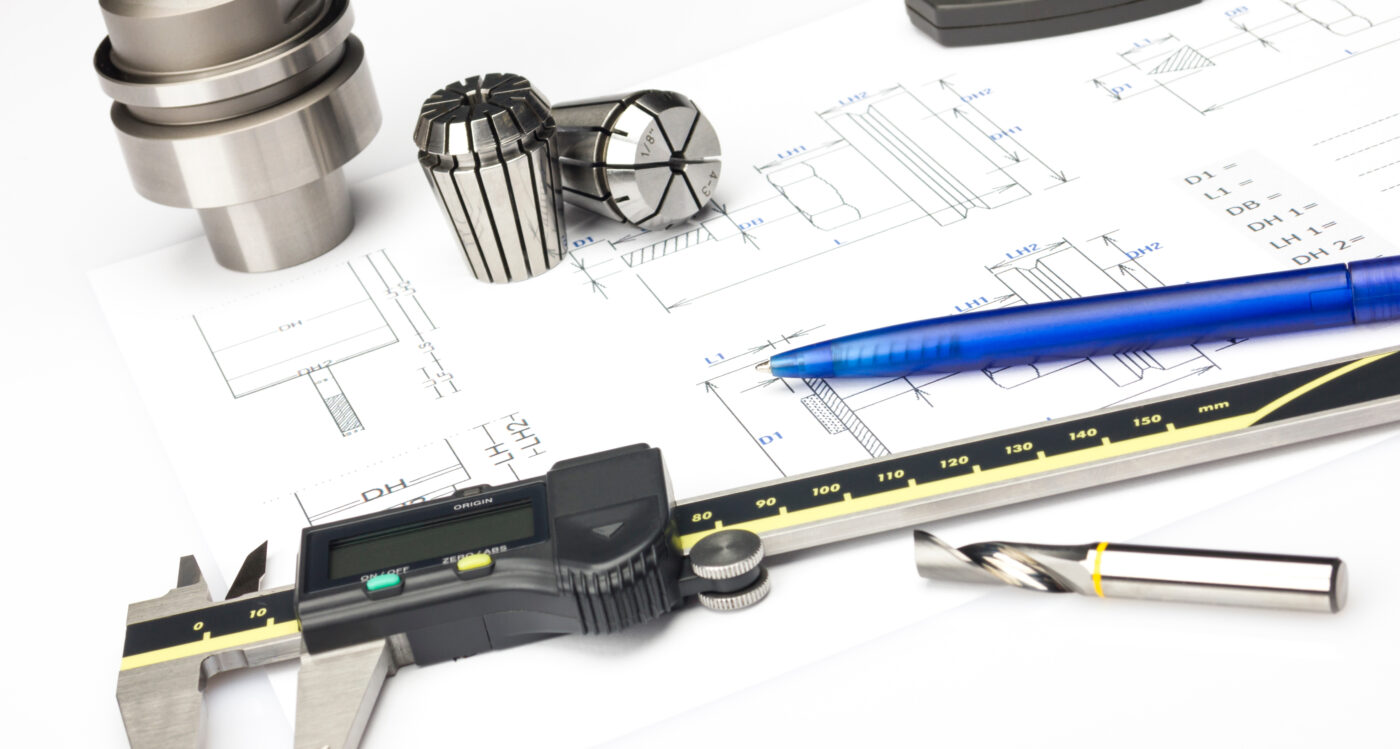
Tool renovation price list:
Price list for grinding of tools | Our price list for tool grinding and coating will inform you how the entire service and service of tools works and what we can offer you.
Povlakování nástrojů
PVD povlaky přináší v průmyslové výrobě a aplikacích mnoho technických, ekonomických i ekologických efektů. Volba povlaku závisí na nástroji a konkrétních podmínkách jeho aplikace. Se správnou volbou povlaku vám pomůžeme. Náš základní sortiment nabídky tvoří 10 typů PVD povlaků. Ten může být rozšířen o řadu zákaznických variant.
Maximizer Pluspovlak TiAlN
|
![]() |
POPIS:Nízké a střední řezné rychlosti: frézování a vrtání. OBLAST APLIKACÍ:Široký rozsah materiálů, excelentní pro vrtání. |
CROSSCUT PLUSpovlak AlCrN
|
![]() |
POPIS:Střední a vysoké řezné rychlosti a rychlosti posuvu: frézování, odvalování. Minimální nebo nízké mazání a chlazení. OBLAST APLIKACÍ:Obrábění náročných materiálů, nerezí, Ni slitin. |
HARDCUT PLUSpovlak TiSiN
|
![]() |
POPIS:Vysokorychlostní obrábění s velmi rychlým posuvem: frézování, odvalování. Za sucha nebo minimum mazání. Vysoké tepelné zatížení. OBLAST APLIKACÍ:Tvrdé materiály (>52 HRC) a Ti slitiny. |
TRIPLECOATING Crpovlak TiN + AlTiN + CrAlSiN
|
![]() |
POPIS:Povlak tvořený adhezní vrstvou TiN, středovou vrstvou AlTiN a vrchní nanokompozitní vrstvou CrAlSiN, který vhodně kombinuje vynikající houževnatost a tvrdost vrstvy AlTiN a extrémněvysokou tvrdost vrchní nanokompozitní vrstvy. OBLAST APLIKACÍ:Obrábění kalených materiálů, nerezí, obrábění těžkoobrobitelných materiálů a velmi náročné aplikace. |
MARWIN SIpovlak TiAlSiN
|
![]() |
POPIS:Nanokompozitní povlak TiAlSiN tvořený základní vrstvou s vysokou tvrdostí a povrchovou vrstvou s vysokou tepelnou i chemickou stabilitou. OBLAST APLIKACÍ:Univerzální povlak se širokou škálou aplikací; frézování, vrtání, vystružování. |
MARWIN Gpovlak TiAlN – AlTiN
|
![]() |
POPIS:Nanovrstevný gradientní systém AlTiN tvořený vrstvou s plynulou změnou složení. OBLAST APLIKACÍ:Univerzální povlak se širokou škálou aplikací; frézování, vrtání, vystružování. |
LUBRIK Gpovlak AlTiN
|
![]() |
POPIS:Povlak tvořený gradientní vrstvou AlTiN zakončený kluznou vrstvou s obsahem oxidů a uhlíku. OBLAST APLIKACÍ:Obrábění barevných kovů; závitování. |
TRIPLECOATING SIpovlak TiN + AlTiN +TiSiN
|
![]() |
POPIS:Povlak tvořený adhezní vrstvou TiN, středovou vrstvou AlTiN a vrchní nanokompozitní vrstvou s vysokým obsahem Si, který vhodně kombinuje vynikající houževnatost a tvrdost vrstvy AlTiN a extrémně vysokou tvrdost vrchní nanokompozitní vrstvy. OBLAST APLIKACÍ:Obrábění zušlechtěných ocelí s tvrdostí nad 60 HRC, obrábění těžkoobrobitelných materiálů, obrábění za sucha či za intenzivních řezných podmínek. |
HARDCUT PLUSpovlak AlCrN
|
![]() |
POPIS:Frézování, odvalování nebo frézování šikmého ozubení. Mokré i suché frézování. OBLAST APLIKACÍ:Obrábění litiny, nástrojové oceli, nerez oceli nebo titanové a niklové slitiny. |
ALWINpovlak CrAlSiN
|
![]() |
POPIS:Nanokompozitní povlak CrAlSiN s vysokým obsahem chromu, vhodný pro aplikace náročné na oxidační odolnost a odolnost vůči nalepování obráběného materiálu na nástroj. OBLAST APLIKACÍ:Lisování, tváření, frézování, vrtání, tlakové lití hliníku. |
TiNpovlak TiN
|
![]() |
POPIS:Povlak tvořený vrstvou TiN pro méně náročné aplikace a nízké řezné rychlosti. OBLAST APLIKACÍ:Vrtání, frézování, komponenty, formy a nástroje. |
To avoid production downtime, we recommend that you plan tool renovations well in advance.
Is the right time to renovate tools right now? Contact us.